Cet article se penche sur le processus de fabrication du polymère super absorbant (SAP).
Note : Les informations techniques avancées présentées dans cet article sont fournies par nos partenaires estimés, les fabricants de polymères super absorbants, avec lesquels nous collaborons étroitement. Pour de plus amples informations, des discussions détaillées ou des questions concernant ce sujet, veuillez remplir le formulaire pour entrer en contact avec notre équipe technique dévouée.
Qu'est-ce que le polymère super absorbant ?
Un polymère super absorbant (SAP) est généralement fabriqué par le processus de polymérisation de l'acide acrylique combiné à de l'hydroxyde de sodium et à un initiateur. Ce processus aboutit à la formation du sel de sodium de l'acide polyacrylique, communément appelé polyacrylate de sodium, qui est le type de SAP le plus largement produit dans le monde.
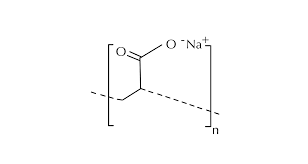
Le polyacrylate de sodium se présente sous la forme de particules cristallines blanches et légères dans des conditions normales. Il possède plusieurs caractéristiques essentielles telles que l'absence d'odeur, la non-toxicité et la légèreté de sa texture. Comparé à d'autres matériaux résineux d'usage général, il est le plus léger par unité de masse et présente des propriétés exceptionnelles d'absorption et de rétention de l'eau.
Outre le polyacrylate de sodium, divers autres matériaux sont utilisés dans la production de polymères superabsorbants. Il s'agit notamment du copolymère de polyacrylamide, du copolymère d'anhydride maléique et d'éthylène, de la carboxyméthylcellulose réticulée, des copolymères d'alcool polyvinylique, de l'oxyde de polyéthylène réticulé et du copolymère de polyacrylonitrile greffé à l'amidon, entre autres. Ce dernier, le copolymère de polyacrylonitrile greffé à l'amidon, est l'une des premières formes de SAP à avoir été mises au point.
Principe
Le principe d'absorption de l'eau de la résine polyacrylique diffère considérablement de celui des autres déshydratants. Elle a la capacité d'absorber l'eau des centaines de fois son propre poids, ce qui entraîne la formation d'un gel. La structure de ce gel est déterminée par les propriétés de réticulation de la résine polyacrylique, ce qui garantit que l'eau ne peut pas être expulsée ou s'écouler au-delà d'un seuil de pression spécifique.
Par conséquent, les polymères d'acide polyacrylique sont des matériaux appropriés pour synthétiser des polymères superabsorbants. Les capacités d'absorption d'eau de ces polymères ne dépendent pas uniquement des matériaux utilisés, mais sont également influencées par le processus de synthèse des polymères superabsorbants.
Le processus de production de la résine superabsorbante suit plusieurs étapes clés
Préparation des ingrédients :
De l'acide acrylique de qualité industrielle, de l'hydroxyde de sodium, du persulfate de sodium comme initiateur et du divinylbenzène comme agent de réticulation sont préparés pour la polymérisation chimique.
Distillation du polypropylène :
Le polypropylène de qualité industrielle subit une distillation sous pression réduite afin d'éviter sa dégradation pendant le stockage et le transport. Un inhibiteur de polymérisation est ajouté pour maintenir ses propriétés de polymérisation. La distillation nécessite l'évacuation de l'air du système pour éviter d'atteindre le point d'ébullition du polypropylène en raison de sa résistance aux basses températures.
Préparation de la solution alcaline :
L'hydroxyde de sodium de qualité industrielle est dissous dans de l'eau distillée pour éliminer les impuretés susceptibles d'affecter le processus de polymérisation du polypropylène. La solution filtrée qui en résulte sert de solution alcaline pour la polymérisation en masse.
Neutralisation :
Le polypropylène distillé est lentement ajouté à la solution d'hydroxyde de sodium pour la neutraliser. La neutralisation optimale se produit à des températures comprises entre 10 et 50°C, l'échange d'ions produisant du sel de polypropylène et de l'eau. Les réactifs sont dosés avec soin pour garantir une réaction et une consommation complètes.
Polymérisation :
Après neutralisation, du persulfate de sodium et du divinylbenzène sont ajoutés pour initier la polymérisation du sel de polypropylène. La polymérisation se produit à des températures ambiantes inférieures à 60°C pendant environ 2 heures, suivies d'une augmentation de la température à 70°C pendant plus de 3 heures pour former un gel de sel de polypropylène. Le gel est séché à 70-80°C pour obtenir une résine d'acide polyacrylique solide, qui est ensuite broyée et moulue en particules de poudre pour une utilisation industrielle.
Ce schéma de processus donne un aperçu concis du processus général de production pour les produits suivants polyacrylate de sodiumune résine superabsorbante couramment utilisée.
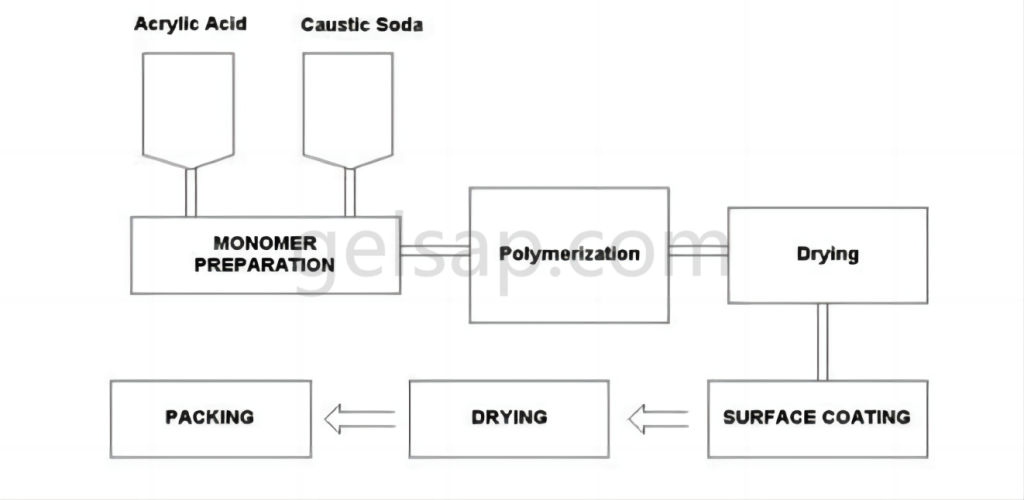
Actuellement, les polymères superabsorbants sont produits à l'aide de quatre méthodes principales : la polymérisation directe, la polymérisation en gel, la polymérisation en suspension et la polymérisation en solution. Chaque méthode offre des avantages distincts et permet d'obtenir des produits de qualité différente.
Polymérisation du gel
La polymérisation en gel par la méthode de l'émulsion inverse consiste à transformer le polypropylène brut en un solvant. Pour ce faire, le polypropylène est dissous dans un solvant non polaire, qui agit comme un agent de dissolution, avec un agent actif huileux pour créer un solvant huileux. Un initiateur et un agent de réticulation sont ensuite ajoutés à cette solution au cours du processus.
La préparation des matières premières suit l'approche consistant à combiner "monomère de polypropylène + solvant huileux contenant un initiateur et un agent de réticulation + lessive". La solution obtenue, composée de polyacrylate insoluble, sert de support au processus de polymérisation du gel.
Description de la méthode:
La méthode consiste à mélanger de l'acide acrylique congelé, de l'eau, des agents de réticulation et des initiateurs UV, qui sont ensuite déposés sur un tapis roulant ou dans de grandes cuves. Ce mélange liquide est transféré dans un "réacteur", une longue chambre équipée de puissantes lampes UV qui stimulent les réactions de polymérisation et de réticulation. Les "billes" de gel collant qui en résultent contiennent de 60 à 70% d'eau.
Ces billes sont ensuite déchiquetées ou broyées et transférées dans divers types de séchoirs. Des agents de réticulation supplémentaires peuvent être appliqués à la surface des particules par le biais d'une "réticulation de surface", ce qui améliore la capacité du produit à gonfler sous la pression, une caractéristique mesurée comme l'absorption sous charge (AUL) ou l'absorption contre la pression (AAP). Après séchage, les particules de polymère sont criblées pour garantir une distribution granulométrique adéquate avant d'être emballées.
La méthode de polymérisation en gel (GP) est actuellement la technique la plus utilisée pour produire des polymères superabsorbants à base de polyacrylate de sodium que l'on retrouve dans les couches pour bébés et autres produits d'hygiène jetables.
Avantage
L'un des avantages de la méthode de polymérisation par émulsion inverse est qu'elle crée une émulsion en mélangeant le solvant non polaire contenant le polypropylène dissous avec le solvant huileux contenant l'initiateur et l'agent de réticulation. Cette émulsion permet au polyacrylate de se polymériser sur la couche externe du solvant polypropylène, formant une structure "huile dans l'eau" qui facilite le processus de polymérisation du polyacrylate.
La structure "huile dans l'eau" isole efficacement la performance libre du polyacrylate, ce qui lui permet de subir une fonction de polymérisation unique. Cela accélère la vitesse de réaction du polyacrylate, rendant la vitesse de préparation de la polymérisation en émulsion inverse cinq fois plus rapide que celle de la polymérisation en solution.
En outre, la présence du milieu de dispersion facilite non seulement le transfert de chaleur et le contrôle de la température, mais permet également la polymérisation de la résine superabsorbante dans des conditions de basse température. Cette méthode permet de surmonter les limitations de température généralement associées aux matériaux de résine polyacrylique.
En outre, la phase huileuse utilisée dans la polymérisation en émulsion inverse peut être réutilisée plusieurs fois. Bien qu'elle ne permette pas de réaliser les mêmes économies que la polymérisation en masse, elle résout le problème du gaspillage excessif de l'initiateur et de l'agent de réticulation, réduisant ainsi les inefficacités en termes de coûts.
Polymérisation en suspension
La polymérisation en suspension partage un principe similaire à celui de la polymérisation en gel, en particulier en ce qui concerne l'utilisation d'un dispersant pour faciliter le transfert de chaleur, la variation du contrôle de la température et l'accélération de la vitesse de réaction de la polymérisation.
Cependant, la différence essentielle réside dans l'utilisation des phases : La polymérisation en suspension utilise la phase aqueuse comme phase séparée et la phase huileuse comme phase continue. Elle suspend le dispersant, dissous dans le polypropylène, sous forme de gouttelettes à la surface de la phase huileuse, où la réaction de polymérisation a lieu à l'intérieur de ces gouttelettes en suspension.
Comme la polymérisation en gel, la polymérisation en suspension transfère efficacement la chaleur du site de réaction grâce à la conductivité thermique du dispersant. Ainsi, la réaction de polymérisation n'est pas limitée par les conditions de température. Pendant la polymérisation, la faible viscosité des substances alcalines et du polypropylène minimise la rétention des impuretés qui n'ont pas réagi.
Avantage
L'un des avantages de la polymérisation en suspension par rapport à la polymérisation en gel est la facilité de récupération du solvant par distillation, avec la possibilité de recycler plusieurs fois la phase huileuse avec un impact minimal sur l'environnement.
Dans la polymérisation en suspension, le réactif à base d'eau est mis en suspension dans un solvant à base d'hydrocarbures. Cette méthode permet la formation de particules de polymère primaire directement dans le réacteur, plutôt que par des processus mécaniques dans des étapes postérieures à la réaction. En outre, des améliorations de performance peuvent être incorporées pendant ou immédiatement après l'étape de réaction.
Il convient de noter que la polymérisation en suspension n'est pratiquée que par un petit nombre d'entreprises en raison de la nécessité d'un contrôle avancé de la production et de l'ingénierie des produits au cours du processus de polymérisation.
Dernières réflexions
Par essence, les polymères superabsorbants représentent un matériau fiable connu pour ses capacités d'absorption et de rétention de l'eau.
Le principe sous-jacent de leur préparation consiste à convertir le polypropylène en sel par réaction alcaline, suivie d'un processus de polymérisation catalysé par un initiateur et un agent de réticulation, ce qui aboutit à la formation de substances polymères.
Dans le contexte industriel, le processus de préparation est classé en quatre catégories en fonction des variations du processus. Chacune de ces méthodes présente ses propres avantages et inconvénients en ce qui concerne les coûts de préparation, la qualité, les processus et la gestion des déchets. Le choix du procédé de préparation doit être déterminé en fonction des exigences spécifiques de l'application de l'acide polyacrylique. resi absorbant l'eaun, en tenant compte de facteurs tels que l'efficacité et l'adéquation.
Pour plus d'informations ou de renseignements sur ce sujet, n'hésitez pas à nous contacter en utilisant le formulaire ci-dessous.