Este artículo profundiza en el proceso de fabricación del polímero superabsorbente (SAP).
Nota: Los avanzados conocimientos técnicos presentados en este artículo han sido proporcionados por nuestros estimados socios, los fabricantes de polímero superabsorbente, con los que colaboramos estrechamente. Para más información, discusiones detalladas o preguntas sobre este tema, rellene el formulario para ponerse en contacto con nuestro equipo técnico especializado.
¿Qué es el polímero superabsorbente?
Un polímero superabsorbente (SAP) se fabrica normalmente mediante el proceso de polimerización de ácido acrílico combinado con hidróxido de sodio y un iniciador. Este proceso da lugar a la formación de sal sódica de ácido poliacrílico, conocida comúnmente como poliacrilato sódico, que es el tipo de SAP más producido a nivel mundial.
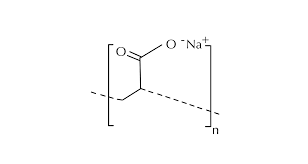
El poliacrilato de sodio aparece como partículas cristalinas de color blanco claro en condiciones normales. Posee varias características clave, como ser inodoro, no tóxico y tener una textura ligera. Comparado con otros materiales de resina de uso general, es el más ligero por unidad de masa y presenta unas propiedades excepcionales de absorción y retención de agua.
Además del poliacrilato de sodio, se utilizan otros materiales en la producción de polímeros superabsorbentes. Entre ellos se encuentran el copolímero de poliacrilamida, el copolímero de anhídrido etilen maleico, la carboximetilcelulosa reticulada, los copolímeros de alcohol polivinílico, el óxido de polietileno reticulado y el copolímero injertado de almidón de poliacrilonitrilo, entre otros. Este último, el copolímero injertado de almidón de poliacrilonitrilo, destaca como una de las primeras formas de SAP desarrolladas.
Principio
El principio de absorción de agua de la resina poliacrílica difiere significativamente del de otros desecantes. Tiene la capacidad de absorber agua cientos de veces su propio peso, lo que da lugar a la formación de un gel. La estructura de este gel viene determinada por las propiedades de reticulación de la resina poliacrílica, lo que garantiza que el agua no pueda salir ni fluir más allá de un umbral de presión específico.
Como resultado, los polímeros de ácido poliacrílico son materiales adecuados para sintetizar polímeros superabsorbentes. La capacidad de absorción de agua de estos polímeros no depende únicamente de los materiales utilizados, sino que también influye el proceso de síntesis de los polímeros superabsorbentes.
El proceso de producción de la resina superabsorbente sigue varios pasos clave
Preparación de los ingredientes:
Para la polimerización química se preparan ácido acrílico de calidad industrial, hidróxido de sodio, persulfato de sodio como iniciador y divinilbenceno como agente reticulante.
Destilación del polipropileno:
El polipropileno de calidad industrial se somete a destilación a presión reducida para evitar su degradación durante el almacenamiento y el transporte. Se añade un inhibidor de polimerización para mantener sus propiedades de polimerización. La destilación requiere evacuar el aire del sistema para evitar alcanzar el punto de ebullición del polipropileno debido a su resistencia a las bajas temperaturas.
Preparación de la solución alcalina:
El hidróxido de sodio de calidad industrial se disuelve en agua destilada para eliminar las impurezas que podrían afectar al proceso de polimerización del polipropileno. La solución filtrada resultante sirve como solución alcalina para la polimerización a granel.
Neutralización:
El polipropileno destilado se añade lentamente a la solución de hidróxido de sodio, neutralizándola. La neutralización óptima se produce a temperaturas entre 10-50°C, intercambiando iones para producir sal de polipropileno y agua. Los reactivos se dosifican cuidadosamente para garantizar una reacción y un consumo completos.
Polimerización:
Tras la neutralización, se añaden persulfato sódico y divinilbenceno para iniciar la polimerización de la sal de polipropileno. La polimerización se produce a temperaturas ambiente inferiores a 60°C durante aproximadamente 2 horas, seguidas de un aumento de la temperatura a 70°C durante más de 3 horas para formar un gel de sal de polipropileno. El gel se seca a 70-80°C para obtener resina sólida de ácido poliacrílico, que después se tritura y se muele en partículas de polvo para uso industrial.
Este esquema del proceso ofrece una visión concisa del proceso general de producción de poliacrilato de sodio, una resina superabsorbente de uso común.
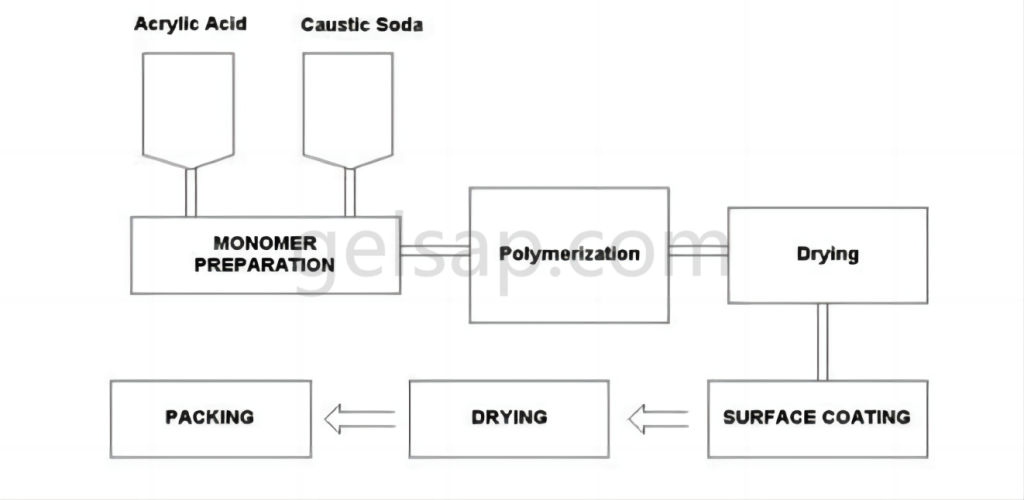
Actualmente, los polímeros superabsorbentes se producen utilizando uno de los cuatro métodos principales: polimerización directa, polimerización en gel, polimerización en suspensión y polimerización en solución. Cada método ofrece ventajas distintas y da lugar a diferentes calidades de producto.
Polimerización en gel
La polimerización en gel mediante el método de emulsión inversa consiste en convertir el polipropileno bruto en una forma disolvente. Esto se consigue disolviendo el polipropileno en un disolvente no polar, que actúa como agente disolvente, junto con un agente activo oleoso para crear un disolvente oleoso. A continuación, se añaden a esta solución un iniciador y un agente de reticulación durante el proceso.
La preparación de las materias primas sigue el planteamiento de combinar "monómero de polipropileno + disolvente oleoso que contiene iniciador y agente reticulante + lejía". La solución resultante, compuesta por poliacrilato insoluble, sirve como medio para el proceso de polimerización en gel.
Descripción del método:
El método consiste en mezclar ácido acrílico congelado, agua, agentes de reticulación y productos químicos iniciadores de UV, que luego se depositan en una cinta móvil o en grandes cubas. Esta mezcla líquida se transfiere a un "reactor", una larga cámara equipada con potentes luces UV que impulsan las reacciones de polimerización y reticulación. Los "troncos" de gel pegajoso resultantes contienen 60-70% de agua.
Posteriormente, estos troncos se trituran o se muelen y se transfieren a diversos tipos de secadoras. Pueden aplicarse agentes reticulantes adicionales a la superficie de las partículas mediante "reticulación superficial", lo que mejora la capacidad del producto para hincharse bajo presión, una característica que se mide como Absorbencia Bajo Carga (AUL) o Absorbencia Contra Presión (AAP). Tras el secado, las partículas de polímero se tamizan para garantizar una distribución adecuada del tamaño de las partículas antes del envasado.
El método de polimerización en gel (GP) es actualmente la técnica más utilizada para producir polímeros superabsorbentes de poliacrilato de sodio que se encuentran en los pañales para bebés y otros productos higiénicos desechables.
Ventaja
Una ventaja del método de polimerización por emulsión inversa es que crea una emulsión mezclando el disolvente no polar que contiene el polipropileno disuelto con el disolvente oleoso que contiene el iniciador y el agente reticulante. Esta emulsión permite que el poliacrilato se polimerice en la capa exterior del disolvente de polipropileno, formando una estructura de "aceite en agua" que facilita el proceso de polimerización del poliacrilato.
La estructura "aceite en agua" aísla eficazmente el rendimiento libre del poliacrilato, lo que le permite someterse a una única función de polimerización. Esto acelera la velocidad de reacción del poliacrilato, haciendo que la velocidad de preparación de la polimerización en emulsión inversa sea cinco veces más rápida que la de la polimerización en solución.
Además, la presencia del medio de dispersión no sólo ayuda a la transferencia de calor y al control de la temperatura, sino que también permite que la polimerización del material de resina superabsorbente se produzca en condiciones de baja temperatura. Este método supera las limitaciones de temperatura típicamente asociadas a los materiales de resina poliacrílica.
Además, la fase oleosa utilizada en la polimerización en emulsión inversa puede reutilizarse varias veces. Aunque puede que no consiga el mismo ahorro que la polimerización a granel, resuelve el problema del desperdicio excesivo de iniciador y agente reticulante, reduciendo así la ineficacia de los costes.
Polimerización en suspensión
La polimerización en suspensión comparte un principio similar con la polimerización en gel, sobre todo en la utilización de un dispersante para facilitar la transferencia de calor, la variación del control de la temperatura y acelerar la velocidad de reacción de la polimerización.
Sin embargo, la diferencia clave radica en el uso de las fases: La polimerización en suspensión emplea la fase acuosa como fase separada y la fase oleosa como fase continua. Suspende el dispersante, disuelto en polipropileno, en forma de gotitas en la superficie de la fase oleosa, donde la reacción de polimerización tiene lugar dentro de estas gotitas suspendidas.
Al igual que la polimerización en gel, la polimerización en suspensión transfiere eficazmente el calor del lugar de reacción gracias a la conductividad térmica del dispersante. Esto garantiza que la reacción de polimerización no se vea limitada por las condiciones de temperatura. Durante la polimerización, la baja viscosidad de las sustancias alcalinas y del polipropileno minimiza la retención de impurezas sin reaccionar.
Ventaja
Una ventaja de la polimerización en suspensión sobre la polimerización en gel es la facilidad para recuperar su disolvente mediante destilación, con la posibilidad de reciclar la fase oleosa varias veces con un impacto medioambiental mínimo.
En la polimerización en suspensión, el reactivo a base de agua se suspende en un disolvente a base de hidrocarburos. Este método da lugar a la formación de partículas de polímero primario directamente en el reactor, en lugar de mediante procesos mecánicos en etapas posteriores a la reacción. Además, se pueden incorporar mejoras de rendimiento durante o inmediatamente después de la etapa de reacción.
Cabe destacar que la polimerización en suspensión es practicada por unas pocas empresas selectas debido a su exigencia de control avanzado de la producción y de ingeniería del producto durante el proceso de polimerización.
Reflexiones finales
En esencia, los polímeros superabsorbentes representan un material fiable conocido por su capacidad de absorción y retención de agua.
El principio subyacente de su preparación implica convertir el polipropileno en una forma salina mediante una reacción alcalina, seguida de un proceso de polimerización catalizado por un iniciador y un agente reticulante, lo que da lugar a la formación de sustancias poliméricas.
En los entornos industriales, el proceso de preparación se clasifica en cuatro tipos en función de las variaciones del proceso. Cada uno de estos métodos tiene su propio conjunto de ventajas e inconvenientes en relación con los costes de preparación, la calidad, los procesos y la gestión de residuos. La elección del proceso de preparación debe determinarse en función de los requisitos específicos de aplicación del ácido poliacrílico resi que absorbe el aguan, teniendo en cuenta factores como la eficacia y la idoneidad.
Si desea más información o realizar alguna consulta sobre este tema, no dude en ponerse en contacto con nosotros a través del siguiente formulario.